Optical Bonding in Membrane Switches and User Interfaces
The type of bonding technology you choose for your membrane switch or HMI are all dependent on the design and product requirements. There are three typical bonding methodologies: liquid optically clear adhesive (LOCA), optically clear adhesive (OCA), and air gap bonding. CSI will work closely with you in the early stages of the product development to offer a custom designed solution to fit your exact requirements.
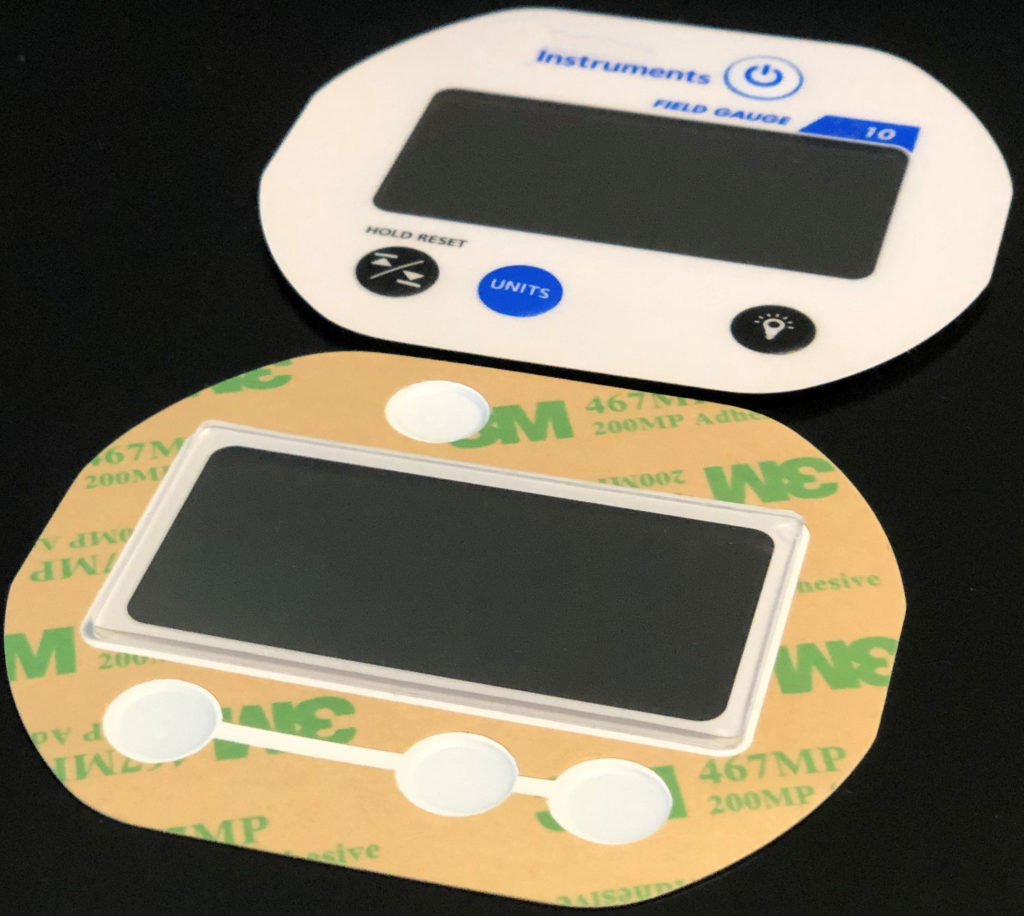
Bonding Options:
Liquid Optically Clear Adhesive (LOCA)
The air gap between the display surface and the rear side of the sensor is filled with a UV liquid adhesive. The adhesive is silicone-free, non-aging and UV stable. The method is typically suitable for TFT displays with frames.
The liquid adhesive is applied over the cover glass and then bonded to the touch panel or TFT panel. The adhesive is spread evenly and bubble-free between the two components. The adhesive is cured without heat using UV light. This prevents.
LOCA offers the most robust and best overall performance of any bonding technology. Handheld devices such as tablets and laptops have led the way using LOCA in display integration. Other industries such as agriculture, military and avionics have incorporated LOCA because of its durability.
Optically Clear Adhesive (OCA)
This is a lamination process with optically clear adhesive (OCA). A lamination from “soft to hard” takes place, e.g. a film-based sensor (ITO / mesh) behind the cover-lense. With the help of storage in an autoclave, the air bubbles are eliminated.
OCA is commonly used on touchscreens, LCD flat panel displays, transparent graphic overlays and other devices requiring an optically clear bond. OCA’s thin, consistent thickness makes it an ideal choice for flexible to rigid bonding and tight tolerance bonding situations. OCA is classified as a dry film, pressure sensitive adhesive and there are different versions depending on the application and substrate to which it will be applied.
Air Gap
In this process, the display is glued with an adhesive frame directly behind the sensor or on the printing of the cover-lense in a clean room. An air gap between the display and the sensor and cover-lense remains. Air bonding is both a simple and cost-effective way to integrate displays with cover-lenses or touch sensors. Depending on the application, the assembly takes place with single adhesive strips or with a closed adhesive frame. Both economical and lightweight, an air gap display construction is a popular option for personal handheld electronics such as smartphones. The layers are integrated with a gasket leaving behind a small air gap.