Epoxy Key Tops for Rubber Keypads
Epoxy key top coating is a protective clear epoxy resin coating applied to only the silicone rubber key tops. This thick coating gives keys a hard plastic feel and glossy appearance. Epoxy coating can extend the longevity of key top artwork as it has abrasion resistance and protects the tops of the keys from chemicals, dirt and oils.
The epoxy key tops can really make your product stand out from the competition as it is more visually appealing than standard rubber key tops. The keys have a plastic appearance but producing the epoxy coated rubber keypads is considerably less cost than manufacturing plastic keys. We recommend epoxy key top coating for keys that receive a high number of actuations or applications that are exposed to abrasion. Additionally, the epoxy coated keys can also be backlit similar to a standard rubber keypad. The rubber is laser etched prior to the epoxy being applied to the key tops.
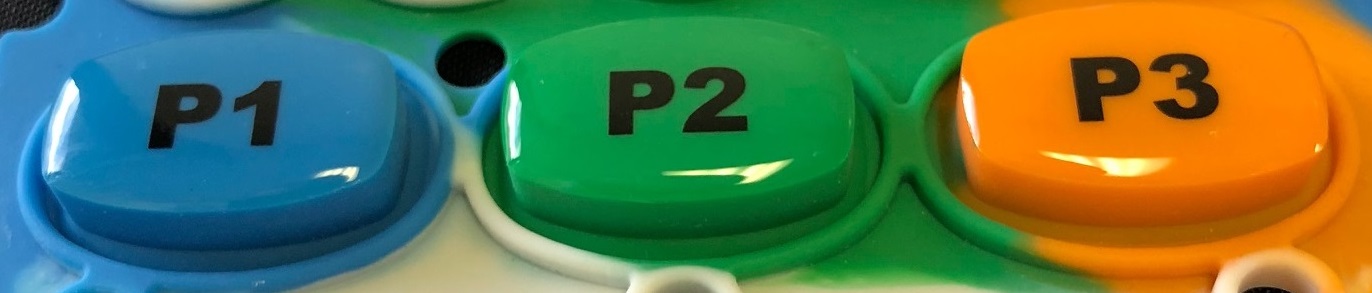
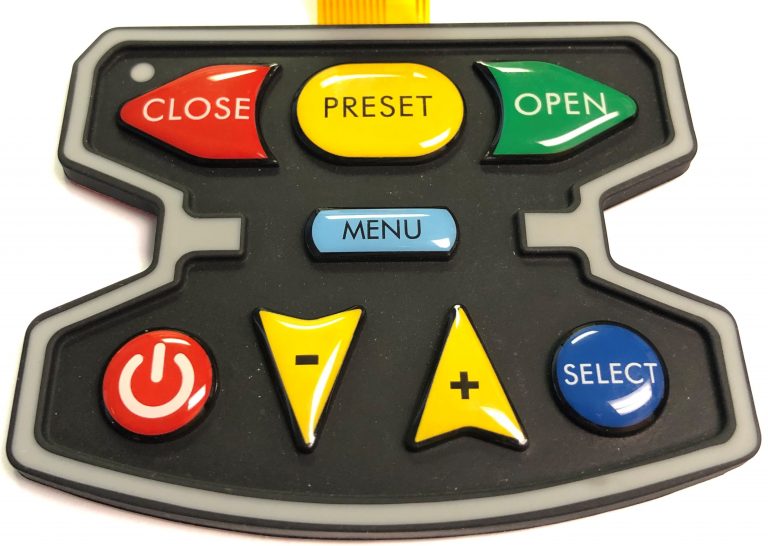