Common Membrane Switch Terminology
ACTUATION FORCE
The pressure required for actuating the circuit of a membrane switch or rubber keypad.
ADHESION
The strength of the molecular attraction bond of one material to another determined by the surface energy in each material.
BACKERS
Incorporating backers into membrane switch assemblies for mounting or rigidity purposes. The most commonly used material is aluminum which can be supplied with a variety of hardware installed. Other backer options include G10, stainless steel, polycarbonate or acrylic materials.
BACKLIGHTING
Lighting of membrane switches using LEDs, light guide film, fiber optics or EL panels.
BREAKDOWN VOLTAGE
The minimum voltage at which the insulation between two conductors begins to fail.
CARBON OVERCOAT
Ink that consists of prepared suspensions of carbon black and is applied over silver circuitry to mitigate the possibility of silver migration. Typically used on the flex tail contacts which is the area on the flex circuit most susceptible to silver migration.
CIRCUITRY
Electrical circuit used to operate a membrane switch typically either printed silver, copper flex or printed circuit board based.
CONDUCTIVITY
A material’s ability to allow the flow of electrons.
COPPER FLEX
A type of circuitry used in membrane switches produced using polyimide (Kapton) as the base material. Manufactured by laminating a thin sheet of copper to a flexible film substrate, the copper is then chemically etched away, leaving the copper traces. An additional layer of polyimide is laminated to the circuit leaving the gold contacts exposed. Also known as Kapton circuits, they have become the superior choice over printed silver especially for outdoor applications due to their excellent dielectric strength, thermal stability, chemical resistance and flexibility.
CROSS-OVER
A conductor intersection where the traces are kept separated and insulated by dielectric material insulator.
DEAD FRONT
A cosmetic feature of a graphic overlay in which an artwork feature is only visible when backlit.
DIELECTRIC / DIELECTRIC INKS
An insulating or non-conducting medium. The inks are used for printing protective patterns on conductive printing to isolate selected areas from electrical contact with other conductors. Typically used for cross-overs and tail insulation.
DOMES
A tactile metal dome (or a snap dome) is a normally open momentary contact that provides a crisp tactile feel letting the user know the button was pressed/actuated. Polydomes can also be utilized if necessary.
DOME RETAINER
An adhesive layer made to hold metal domes in the key-switch.
EMBOSS
Method of raising an aspect or aspects of the overlay material to accentuate key surfaces through mechanical and thermoforming of graphical features. Typically used for keys and/or LED indicators.
ENVIRONMENTAL SEALING
Utilizing proprietary design features in order to seal a membrane switch or rubber keypad. Such features include frame sealing, the use of copper flex circuitry and rubber gasketing.
GRAPHIC OVERLAY
The decorative front layer of a membrane switch or control panel.
KEY HEIGHT
The distance from the highest point of a key to the base of the keypad.
LIGHT EMITING DIODE (LED)
Assembled to the membrane switch circuitry to illuminate a feature or features on the keypad.
PINOUT
The schematic that describes the circuit output requirements for membrane switches. Also known as a wire diagram.
PRESSURE SENSITIVE ADHESIVE (PSA)
Adhesive materials that bond through the application of pressure without the need for heat or solvents.
REAR PSA
A pressure sensitive adhesive applied to the back of a membrane switch for mounting purposes. Different types of rear PSA can be utilized depending on the application and bonding surface.
SHIELDING
Utilizing methods for incorporating ESD/RFI/EMI shielding within the membrane switch layers.
SECOND SURFACE PRINTING
Practice of printing a graphic overlay from the bottom in reverse, so the outer layers protect the graphic. This is particularly useful in membrane switch applications where the graphic overlay experiences abrasive wear.
SILVER INKS
Tiny particles of actual silver suspended in various substrates that produce conductive patterns on rigid and flexible substrates.
SPACER LAYER
A membrane switch adhesive layer separating the electronic circuit layers with button/switch openings.
TAIL BREAKOUT
The location of the tail exit on the back of the membrane switch.
VENTING
Membrane switch openings connected to one another to seal the switch from moisture and other contaminants without venting externally. External venting is also an option if the design allows for it.
WINDOWS
Utilizing the base clear overlay to incorporate windows in a membrane switch typically for displays. Can utilize hardcoats or textures depending on the application. Incorporating a reinforced opti-bond window is also a common technique for windows susceptible to excessive abuse.
WIRE DIAGRAM
A diagram showing the desired connections to the pinout connector.
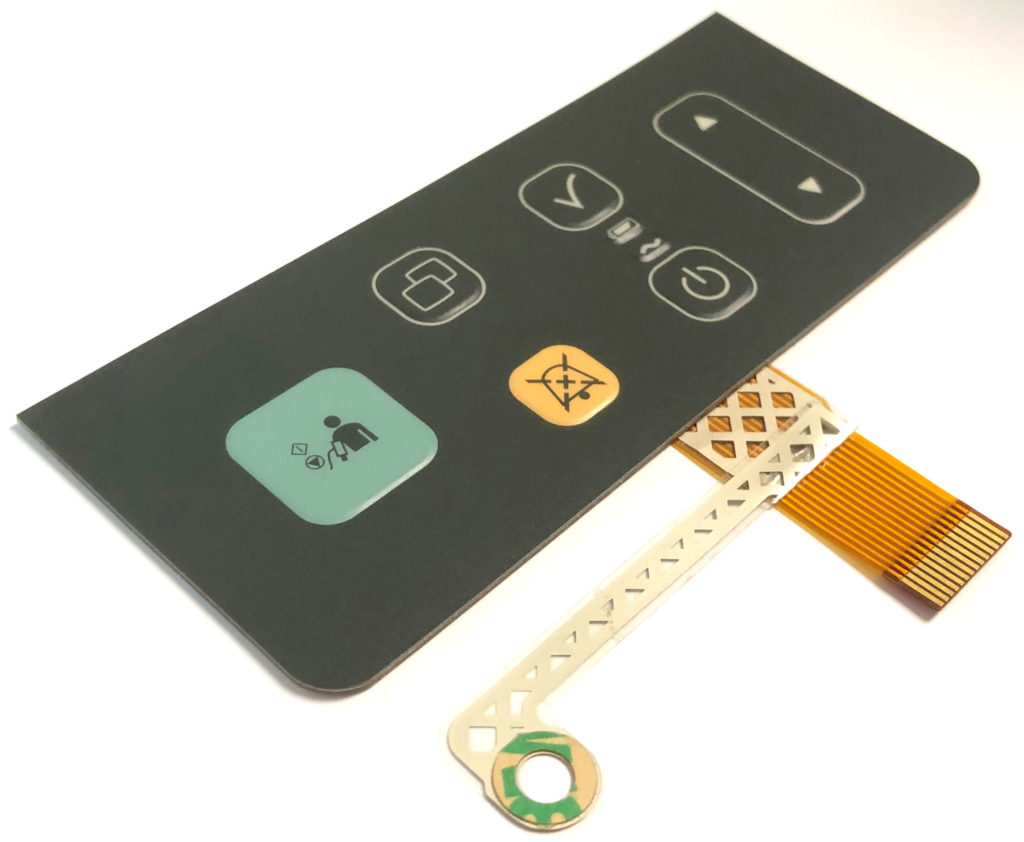
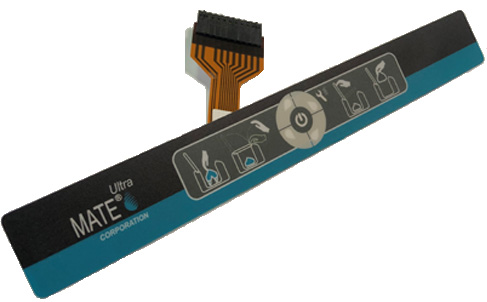
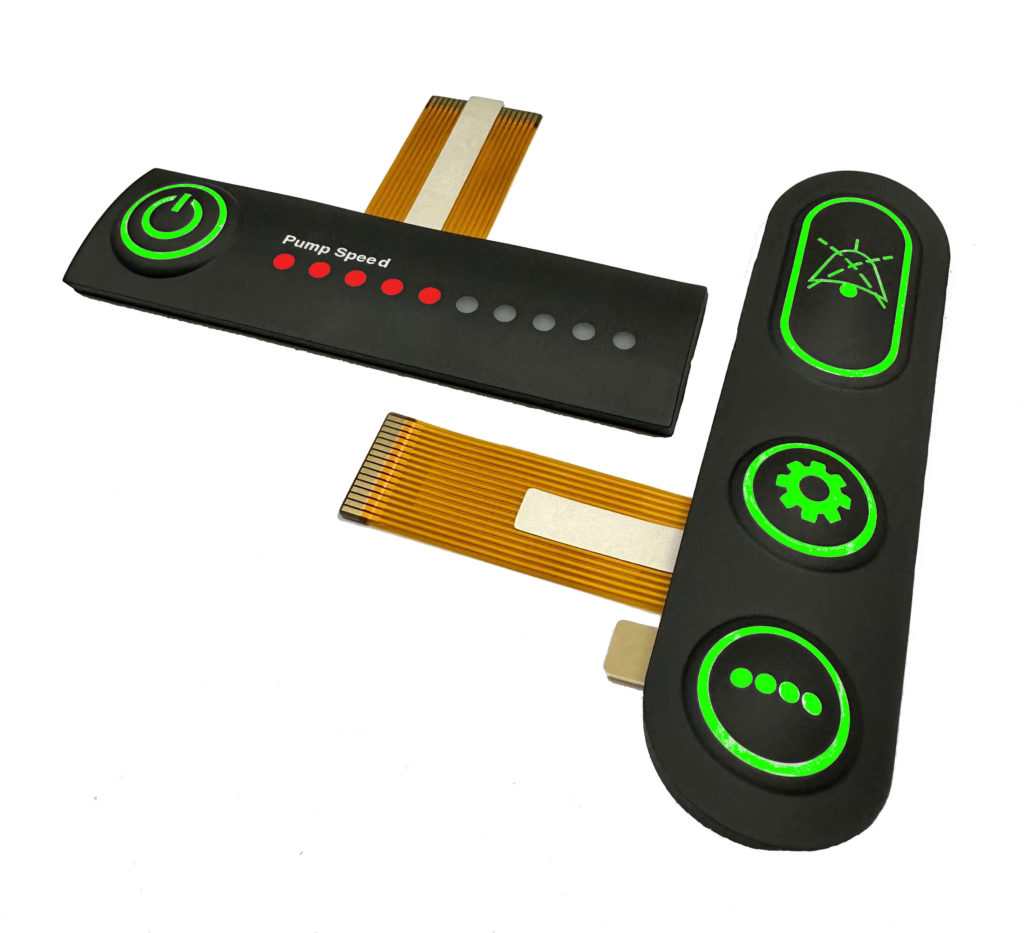
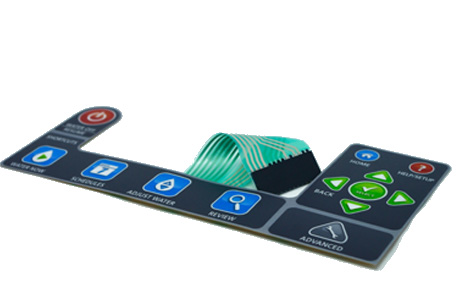
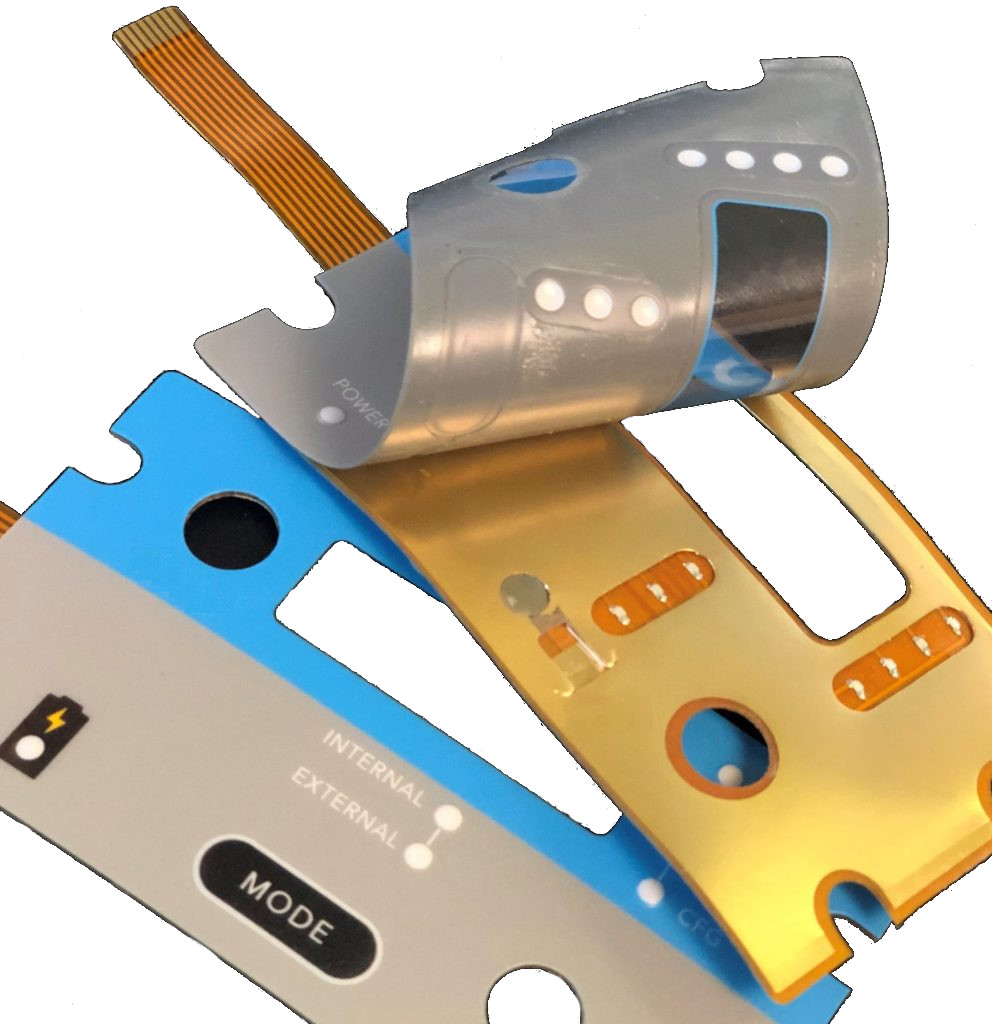
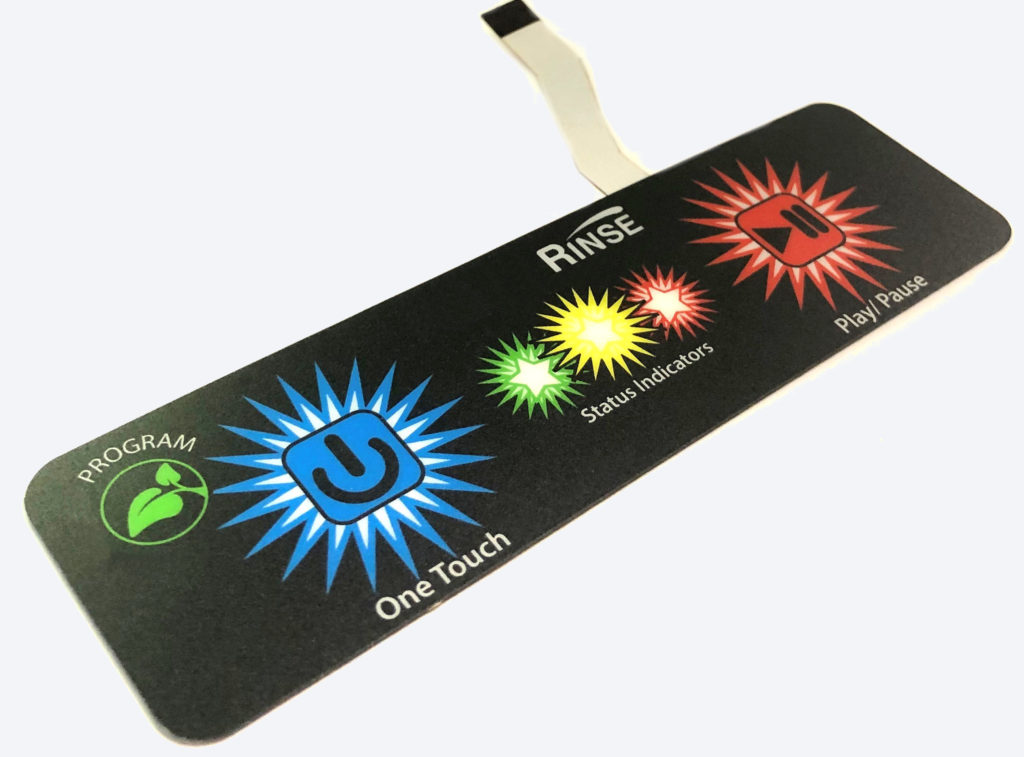

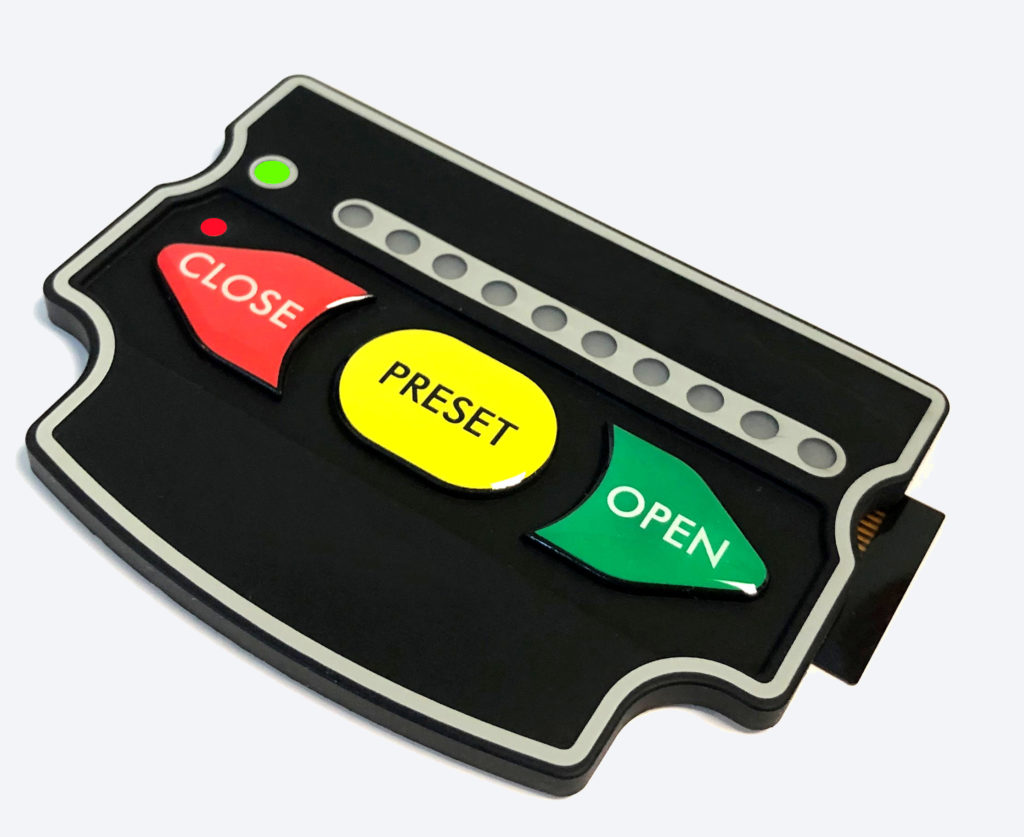