Designing a Waterproof (IP67) Membrane Switch
Many customers reach out to CSI Keyboards with a waterproof IP67 requirement for their membrane switch or user interface. CSI utilizes a few different design techniques in order to waterproof a membrane switch which include utilizing a frame seal gasket, the use of copper flex circuitry, and the use of high performance adhesives. There are other methods and ways of waterproofing that can also be integrated into the design, but the frame seal, the type of circuitry and the adhesive used are the foundation to ensuring that your keypad is environmentally sealed.
The Achilles heel for membrane switch sealing is most always the flex tail breakout area. The tail typically breaks out of the rear of the switch and because the tail is made of the same material as the circuit, a filler piece replaces the ribbon cable shape in the materials of the membrane switch. The gaps on either side of this tail filler is typically where moisture can enter the membrane switch.
A gasket or perimeter seal frame design can solve this problem. A membrane switch with a gasket or perimeter seal does not have a tail filler therefore there is no direct pathway for liquid ingress. CSI Keyboards’ perimeter seal frame switches have proven to be as robust as other sealing methods such as perimeter temperature sealing and can be included in your design at minimal additional cost.
- Construction Concept: Setting the membrane switch circuit within a frame seal gasket, protecting it from the environment.
- Width & Thickness: The thickness of the membrane switch whereby the switch layer printing thickness also taken into consideration, should flush with the gasket making them even as a whole. One whose height is greater than the gasket will budge & cause delamination over time between the product & the interfacing panel, eventually water leakage. The width of the frame seal gasket is also a critical factor dictating the strength of water immerse pressure protection.
- Gasket Adhesive Tape Selection: Not neglecting the gasket, industrial closed cell foam carrier tapes are among the options providing superb adhesion strength.
- Enhancement: For an even more stringent environmental requirement, the conductive printed PET can be substituted with a double-sided through-hole, single conductive print design where the insulator between the two conductive print is the substrate itself, posing an advantage over the insulating dielectric print depreciation between conductive prints of a single sided design when functioning in a high humidity environment.
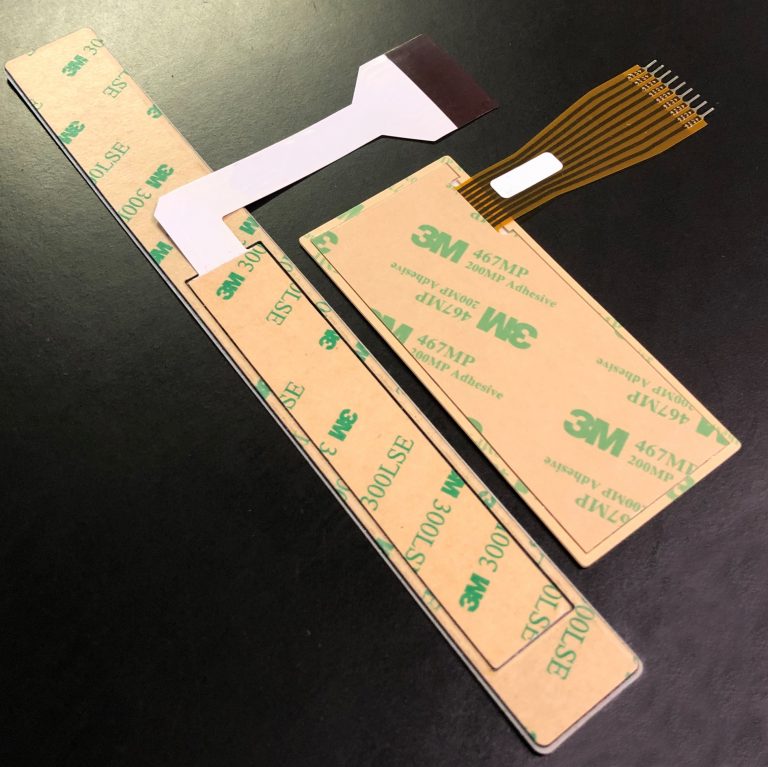
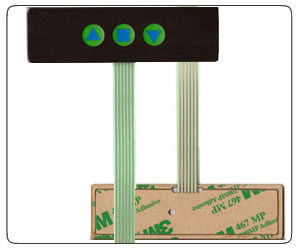
Copper Flex Circuitry:
CSI Keyboards uses copper flex circuitry in the majority of our custom keypad designs due to its excellent dielectric strength, thermal stability, chemical resistance and flexibility. Copper flex, also known as Kapton circuits, have become the superior choice over printed silver especially for outdoor applications.
A printed silver circuit can be replaced with a copper and polyimide construction with minimal additional cost. Copper flex circuitry construction designs offer a significant advantage over printed silver. Additional information on the benefits of copper flex circuity can be found here: Benefits of Using Copper Flex Circuitry vs. Printed Silver.
Copper Flex membrane switch panels are produced using polyimide (Kapton) as the base material. Copper flex keypad switches are manufactured by laminating a thin sheet of copper to a flexible film substrate. The copper is then chemically etched away, leaving the copper traces. An additional layer of polyimide is laminated to the circuit leaving the gold contacts exposed.
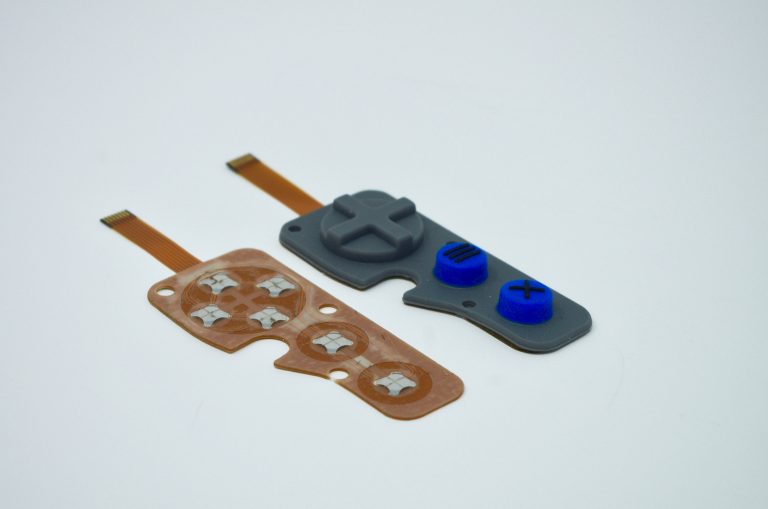