The CSI Process
Concept: The process typically starts with a customer concept which can range from something as simple as a description or a sketch with a list of requirements right up to full keypad drawings.
Design: Once we have enough information on the design, we work up a quote and proposal for the project. CSI then works on a drawing package which typically takes about 2 weeks depending on complexity of design. During those two weeks, we are interfacing back and forth with customer.
Prototype: Once customer signs-off on the design, we built prototype parts which takes about 4-5 weeks. Because it’s a custom product, there are usually some minor tweaks that take place during the prototype stage such as tactile feel of keys, colors, etc.
Production: After prototypes are approved, we enter into production.
Logistics: Work closely with our customer’s procurement team to ensure the customer receives the product when and where they need it.
Sustainability: After the part has entered into production, CSI sustains and supports the user interface throughout the life of the product. CSI is still supporting products that were originally designed 37 years. Some products having gone through some design improvements, while others being built exactly as they were in 1983.
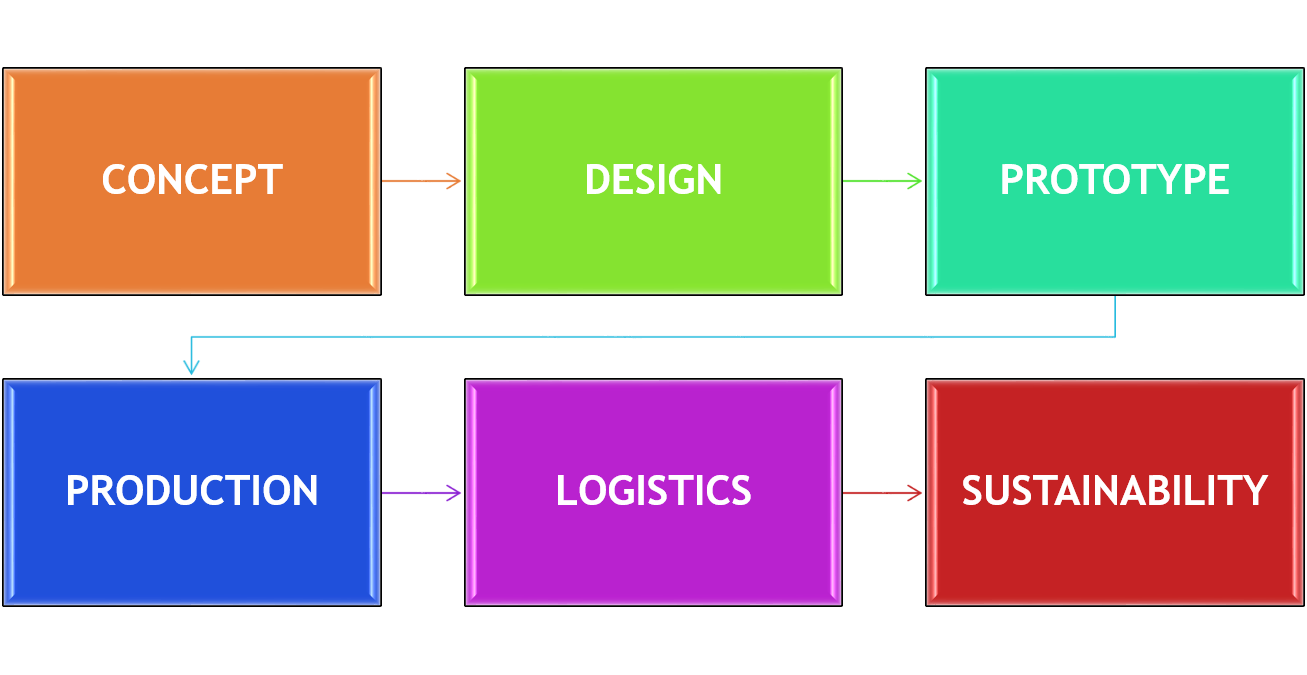